|
Saji A Kuriakose |
|
|
|
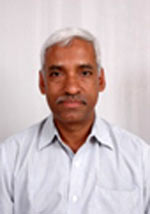
Time:
Tuesday, 1 April 2014
1445 - 1505
ElectroOptical Payloads for Earth and Planetary Observation |
Deputy
Director, Sensors Development Area, Space Applications
Centre,
Ahmedabad
Major achievements:
He has contributed to the design and development of
Electro-optical Sensors for Remote Sensing, planetary and
Meteorological payloads. He was responsible for the optical
design of payloads for INSAT 2A, INSAT 2E, Kalpana, IRS
1C/1D, Resourcesat 1/2, Technology Experiment Satellite (TES),
Cartosat-1 and Cartosat-2 series of satellites. He guided
the teams in the design and development of payloads for
Chandrayaan-1, Indian Mini-satellite, Oceansat-2,
Resourcesat-2, Youthsat and INSAT-3D. He is presently
involved in the development of Sensors for Geo- Imaging
satellite, Chandrayaan-2, Carto-2C/D, Mars Orbiter Mission,
Cartosat-3, Resourcesat-3, and Oceansat-3. He has actively
contributed to the miniaturization of systems. He is
presently the Deputy Director, Sensors Development Area. He
received the space gold medal of the Astronautical Society
of India 2001, as well as ISRO team excellence awards for
Cartosat-2 and Chandrayaan-1 development. |
|
|
|
Abstract |
|
Space Applications Centre, ISRO, has extensive experience in the development of electrooptical sensors for the observation of Earth (land, ocean, and atmosphere) and Moon from space in a variety of spectral bands. At present, SAC is working on a number of increasingly sophisticated instruments for the detailed observation of Earth, Moon, Mars and other planets, as well as the Sun. This talk deals with some of the aspects of electrooptical payload development and the testing carried out.
The challenges in design and realisation of electro-optical payloads are related to application specific mission requirements, satellite orbit selection and constraints, satellite resource constraints (attitude, power, volume, thermal, data transmission capabilities, reliability requirements (life, confidence etc.), and technologies available at present (components, materials, fabrication and test methods etc.). The optical properties of the atmosphere, mainly scattering and absorption of light affect the quality of observation. The configuration of the electro-optical sensor is arrived at after carrying out tradeoff studies at system level and subsystem level, and usually several competing configurations may be available. The most optimum system design in terms of performance, size, weight and electrical power required is chosen for further consideration. Major parameters such as orbit selection, satellite attitude requirements (3 axis stabilized/ spin stabilized etc, attitude control and its accuracy), spacecraft bus requirements (power, transmission band width etc.) selection of sensor type (Electro-optical/ microwave, radio etc), spectral bands (spectral region etc.) are required to be finalized for concluding the overall sensor system specifications.
After the configuration is finalised, detailed designs are initiated; the challenges include the selection of space worthy components and materials, their availability in the required quality and also appropriate fabrication and assembly technologies. During the realisation process, the increased challenges in supply and schedules due to deviations arising in out of tolerances in the components/ fabrication/ assembly process. The available hardware will be different from the theoretical estimation based on catalogue values, so it is essential to resolve very carefully the deviations based on understanding/ estimation of interaction/ impact at subsystem and system level. The equally important, but often unnoticed challenges are present in the design, development, and realisation of test systems, integration and checkout of the sensors. Several challenges experienced during qualification of subsystems and systems, integration activities and ground calibration have to be overcome. The current payloads are very complex and highly sensitive, so the challenge lies in theoretical modeling of the sensors, developing data products and finally in deriving the application specific physical parameters from the data.
The challenges in realization of spaceborne payloads include the requirement for robust designs, choice of suitable materials and components for space use, appropriate fabrication methods, process qualification, and environmental tests to be carried out at qualification level as well as acceptance levels. The sensor development requires multidisciplinary activities to be concurrently carried out, and a very good understanding of the interface aspects is required. The final performance of the sensor system is more complex than that of the subsystems alone. The teams carrying out the developmental activities require very good knowledge of the subsystems as well as the integrated payload. All activities are carefully planned and interface definition is carried out at an early stage of the project.
The design, development and realisation of application specific sensors are dictated by the demanding functionality of the sensor. Initial clarity regarding the user requirements and the purpose is essential for the successful development of the sensor. The requirements of application specific sensors call for innovative ideas and development of new technologies which enable them to be smaller, and lighter, with frugal power requirements. Space Applications Centre has been responsible for the development of a number of Application Specific Sensors since the nineteen seventies.
|
|